ANSYS高效能仿真软件精准模拟驱动未来科技创新发展
adminc2025-03-27装机必备13 浏览
虚拟仿真能否完全替代物理实验?一场技术革命的争议与答案
在传统工业研发中,物理实验一直是验证设计可靠性的“金标准”。随着产品复杂度飙升,高昂的试验成本、漫长的周期以及难以复现极端工况等问题日益凸显。有人质疑:虚拟仿真是否真能替代物理实验?这场争议的答案,或许就藏在ANSYS高效能仿真软件精准模拟驱动未来科技创新发展的技术实践中。
1. 复杂系统设计:如何突破极限?
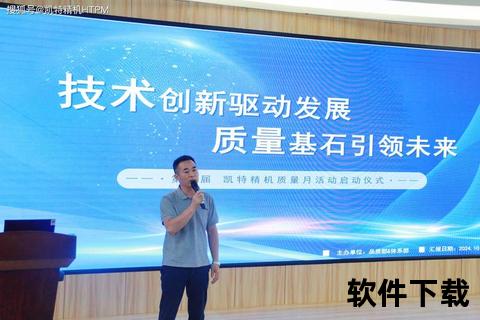
现代工程系统如新能源汽车、航空航天器等,往往涉及多学科耦合与极端环境下的性能挑战。以新能源汽车动力电池为例,其热失控、结构强度、振动疲劳等问题直接关乎安全性与寿命。
案例支撑:某车企在电池包研发中,利用ANSYS对铝制容器进行结构强度仿真,输入内压载荷与材料参数后,仅需数小时便精准预测了焊缝强度极限和爆破压力,相比传统试验节省了70%的耗时。针对电池热失控场景,ANSYS通过CFD模型模拟了电芯温度场的“多米诺效应”,结合实验数据快速定位散热瓶颈,最终优化铝合金垫板设计,使模组温差降低15%。
这类案例表明,ANSYS高效能仿真软件精准模拟驱动未来科技创新发展,不仅突破了物理实验的时空限制,更在复杂系统中实现了“先验优化”,将试错成本压缩至最低。
2. 多物理场耦合:如何实现真实世界的数字化映射?
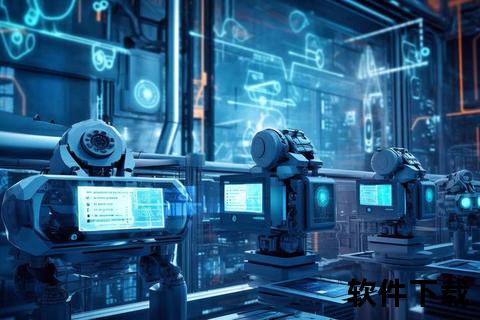
现实世界的工程问题往往涉及结构、流体、电磁等多物理场相互作用。例如,5G通信设备的射频干扰、芯片动态压降等难题,单一物理场分析难以捕捉全貌。
案例支撑:在半导体领域,ANSYS 2022 R1版本的RedHawk-SC SigmaDVD技术,将芯片最坏情况下的动态压降分析从数周缩短至数小时,帮助英特尔等企业提前规避了数十亿美元量级的流片风险。而在航空航天领域,ANSYS Fluent新增的超音速流专用工作空间,通过多场耦合仿真优化了飞机气动外形,使某型号客机燃油效率提升了8%。
这类技术突破依赖于ANSYS的多场协同求解能力。例如,某企业研发的高铁轴承,需同时考虑摩擦热、结构应力与润滑流体的相互作用。ANSYS通过热-力-流耦合模型,模拟了极端载荷下的磨损趋势,最终将轴承寿命预测误差控制在5%以内。
可见,ANSYS高效能仿真软件精准模拟驱动未来科技创新发展,正以“数字实验室”的形式,将多物理场的复杂性转化为可量化、可迭代的设计参数。
3. 工业4.0时代:如何构建数字孪生闭环?
工业4.0的核心是信息物理系统(CPS),而数字孪生技术正是连接虚实世界的纽带。如何让数字模型贯穿产品全生命周期,仍是许多企业的痛点。
案例支撑:宝马集团在电动车电驱系统开发中,利用ANSYS构建了从电机电磁设计到控制器嵌入式代码验证的数字孪生链。通过虚拟调试提前发现软件逻辑错误,使开发周期缩短40%。施耐德电气则将ANSYS仿真数据与物联网结合,对配电设备进行实时健康监测,实现故障预测准确率超90%。
更前沿的应用来自核电站安全壳设计。通过ANSYS Mechanical和LS DYNA的联合仿真,工程师在虚拟环境中复现了飞机撞击、地震波叠加等极端工况,精准评估了混凝土结构的裂纹扩展路径,为安全标准制定提供了关键依据。
这些实践印证,ANSYS高效能仿真软件精准模拟驱动未来科技创新发展,不仅服务于产品研发阶段,更延伸至运维、回收等全生命周期,形成“设计-验证-优化”的闭环。
从争议到共识:企业如何拥抱仿真革命?
虚拟仿真虽无法完全替代物理实验,但已成为技术创新的核心驱动力。对于企业而言,需采取以下策略:
1. 分层应用:在概念设计阶段优先采用仿真筛选方案,在关键验证环节保留必要物理试验,形成“仿真为主、试验为辅”的混合模式。
2. 平台整合:将ANSYS与PLM、IoT平台对接,构建从虚拟验证到实体运维的数据流闭环。
3. 人才培养:建立跨学科的仿真工程师团队,重点提升多场耦合建模与数字孪生应用能力。
未来,随着AnsysGPT等AI工具的引入,仿真技术将进一步降低使用门槛。但技术背后的逻辑始终不变:ANSYS高效能仿真软件精准模拟驱动未来科技创新发展,本质是让人类以更低的成本、更快的速度逼近物理世界的真理。这场争议的终局,或许不是“替代”,而是“融合”——虚拟与现实的交响,终将奏响工业文明的新乐章。